Research: Fracture of lightweight materials
Goal: Research in lightweight materials has three objectives:
- To develop a microstructure-based modeling framework that can predict material flow and fracture for advanced high strength steels and high strength aluminum alloy
- To improve the properties of these materials by manipulating their microstructure
- To implement microstructure-based information into material models used for CAE simulations of forming and vehicle crash
Background: Steels and aluminum alloys currently used for body structure generally fail by plastic instability before fracture occurs. In newer, high strength steels and alloys (now approaching 1500 MPa for steels and 500 MPa for aluminum) however, the usable ductility of these materials decreases, and fracture may precede plastic instability. This competition between plastic instability and fracture needs to be understood to design optimal structural parts that fully exploit the benefits from the high strength.
The multiphase stochastic microstructure of these advanced materials and the interaction of the various phases with their individual deformation characteristics makes modeling their plasticity and fracture behavior complicated. The properties of steel, for example, are controlled by the stability and volume fraction of the retained austenite and the volume fraction and strength of the hardening phases like martensite and bainite. The competing effects of the hardening behavior of these individual phases influence its plasticity and fracture behavior. Fracture models of the ultra-high strength steels, for example, are unavailable in the CAE database. Quantitative linkages between microstructure and macroscopic mechanical properties are mostly non-existent. The current approach to fracture model development for metal sheet alloys used in automotive applications requires expensive testing of both ligament-type and biaxial tension test specimens extracted either from the as-received sheet material or stamped components. This enables a mapping of fracture strains to relevant load conditions resulting in a damage or fracture locus in terms of stress triaxiality. The fracture locus is then used to calibrate a phenomenological fracture model, e.g. the “Generalized Incremental Stress State dependent damage Model” (GISSMO), for implementation into commercial CAE codes. Unfortunately, the current experimental approach is both time consuming and costly since it must be conducted for each material of interest and adequate damage locus sampling is dependent upon the individual stress triaxialities considered. Moreover, accurate accounting for the effect of microstructural mechanisms, such as martensitic transformation, on crack and void nucleation, is not guaranteed (or considered).
Approach: Initial research performed by the GM/Brown CRL demonstrated that microstructure-based simulations have the potential to reduce the cost of calibrating phenomenological fracture models such as GISSMO. The general approach is illustrated in the figure below
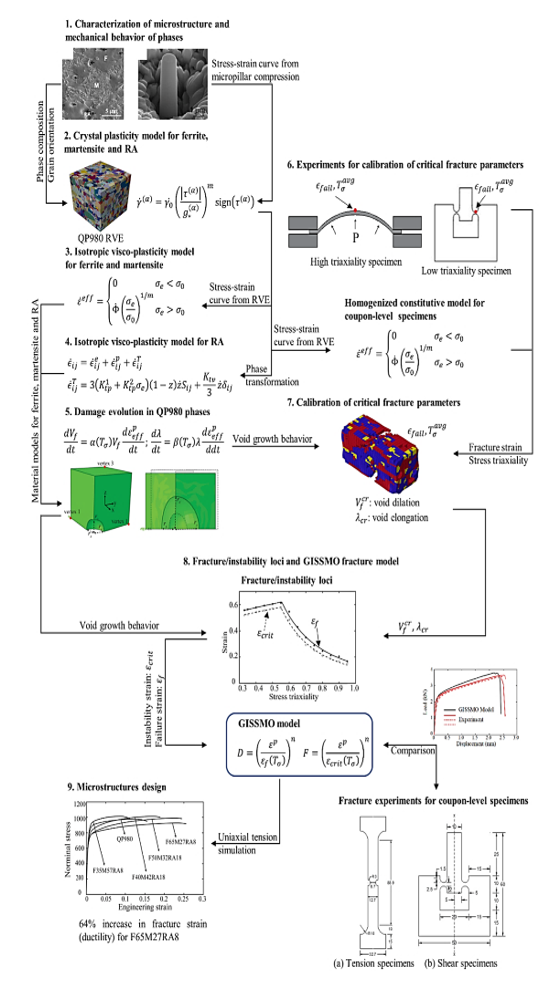
To predict the strength and fracture resistance of a three-phase steel of interest,
- Micropillar compression tests are used to measure the stength of the phases (ferrite, martensite and retained austenite) in the steel
- The material properites in crystal plasticity models of the phases are determined by fitting model predictions to the micropillar compression data
- The crystal plasticity models are used to predict stress-strain curves for polycrystals of the three phases.
- The predictions from (3) are used to determine hardening relations in simpler isotropic models of the phases.
- The rate of growth of voids with plastic strainin is computed for each phase in the steel. The results of these computations are used to calibrate a phenomenological damage model for the phases.
- Two experiments are conducted to measure the critical strains that cause fracture in the steel at high and low stress triaxialities
- The experimental data are used to determine the critical void volume fraction and critical void elongation at the point of void coalescence (which causes a complete loss of strength)
- The calibrated fracture model is used to predict the critical strains at the onset of material instability as a function of stress triaxiality (the fracture locus). These predictions are used to calibrate the failure criteria in the GISSMO phenomenological fracture model.
- The GISSMO is then used to predict fracture in components of interest as a function of strain path. By changing the microstructure in the simulations, the stress-strain curves and fracture strains for new steel microstructures can also be predicted.
The microstructure-informed GISSMO model for QP980 steel was found to predict fracture strains within 18% of experimental measurements of ligament-type test specimens. While these preliminary results are encouraging, further research is required to expand the developed method to ensure both accuracy and robustness as applied to microstructures of steels of relevance to GM. Accordingly, the goals of this project will be to improve the accuracy of physics-based fracture models for both multiphase ultra-high-strength steels and aluminum alloys for further vehicle lightweighting. These models will be used to calibrate fracture criteria for steels and aluminum alloys that are both in current use, and those that are being considered for future use.