Chapter 7
Stress-Strain
relations for linear elastic materials
You
are probably familiar with the behavior of a linear elastic material from
introductory materials courses.
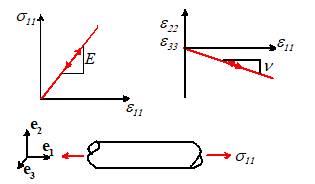
7.1 Isotropic, linear elastic material behavior
If
you conduct a uniaxial tensile test on almost any material, and keep the stress
levels sufficiently low, you will observe the following behavior:
The specimen deforms reversibly: If you remove the loads, the solid returns to
its original shape.
The strain in the specimen depends only on the
stress applied to it it doesn’t depend on the rate of loading, or
the history of loading.
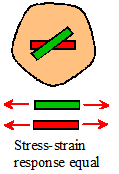
For most materials, the stress is a linear
function of strain, as shown in the picture above. Because the strains are small, this is true
whatever stress measure is adopted (Cauchy stress or nominal stress), and is
true whatever strain measure is adopted (Lagrange strain or infinitesimal
strain).
For most, but not all, materials, the material
has no characteristic orientation. Thus,
if you cut a tensile specimen out of a block of material, as shown in the
figure, the the stressstrain curve will
be independent of the orientation of the specimen relative to the block of material. Such materials are said to be isotropic.
If you heat a specimen of the material,
increasing its temperature uniformly, it will generally change its shape
slightly. If the material is isotropic
(no preferred material orientation) and homogeneous, then the specimen will
simply increase in size, without shape change.
7.2 Stressstrain relations
for isotropic, linear elastic materials. Young’s Modulus, Poissons ratio and the
Thermal Expansion Coefficient.
Before writing down stressstrain relations,
we need to decide what strain and stress measures we want to use. Because the model only works for small shape
changes
Deformation is characterized using the
infinitesimal strain tensor defined in Section 4.6. This is convenient for calculations, but has
the disadvantage that linear elastic constitutive equations can
only be used if the solid experiences small rotations, as well as small shape
changes.
All stress measures are taken to be
equal. We can use the Cauchy stress as the stress measure.
You probably already know the stressstrain relations
for an isotropic, linear elastic solid.
They are repeated below for convenience.
Here, E and are Young’s modulus and Poisson’s ratio, is the coefficient of thermal expansion, and is the increase in temperature of the
solid. The remaining relations can be
deduced from the fact that both and are symmetric.
The inverse relationship can be expressed as
HEALTH
WARNING: Note the factor of 2 in the strain vector. Most texts, and most FEM codes use this
factor of two, but not all. In addition,
shear strains and stresses are often listed in a different order in the strain
and stress vectors. For isotropic
materials this makes no difference, but you need to be careful when listing
material constants for anisotropic materials (see below).
We
can write this expression in a much more convenient form using index notation. Verify for yourself that the matrix
expression above is equivalent to
The inverse
relation is
The stress-strain relations are often expressed using the elastic modulus tensor or the elastic
compliance tensor as
In terms
of elastic constants, and are
7.3 Reduced stress-strain equations for plane
deformation of isotropic solids
For plane strain or
plane stress deformations, some
strain or stress components are always zero (by definition) so the
stress-strain laws can be simplified.
For a
plane strain deformation . The stress strain laws are therefore
In index
notation
where Greek
subscripts can have values 1 or 2.
For a
plane stress deformation
7.4 Representative values for density, and elastic constants of isotropic
solids
Most
of the data in the table below were taken from the excellent introductory text
`Engineering Materials,’ by M.F. Ashby and D.R.H. Jones, Pergamon Press. The remainder are from random web pages…
Note the units values of E
are given in ;
the G stands for Giga, and is short for . The units for density are in - that’s Mega grams. One mega gram is 1000 kg.
Material
|
Mass density
|
Youngs Modulus
|
Poisson Ratio
|
Expansion coeft
|
Tungsten Carbide
|
14 17
|
450650
|
0.22
|
|
Silicon Carbide
|
2.5 3.2
|
450
|
0.22
|
|
Tungsten
|
13.4
|
410
|
0.30
|
|
Alumina
|
3.9
|
390
|
0.25
|
|
Titanium Carbide
|
4.9
|
380
|
0.19
|
|
Silicon Nitride
|
3.2
|
320 - 270
|
0.22
|
|
Nickel
|
8.9
|
215
|
0.31
|
|
CFRP
|
1.5-1.6
|
70 200
|
0.20
|
|
Iron
|
7.9
|
196
|
0.30
|
|
Low alloy steels
|
7.8
|
200 - 210
|
0.30
|
|
Stainless steel
|
7.5-7.7
|
190 - 200
|
0.30
|
|
Mild steel
|
7.8
|
196
|
0.30
|
|
Copper
|
8.9
|
124
|
0.34
|
|
Titanium
|
4.5
|
116
|
0.30
|
|
Silicon
|
2.5-3.2
|
107
|
0.22
|
|
Silica glass
|
2.6
|
94
|
0.16
|
|
Aluminum & alloys
|
2.6-2.9
|
69-79
|
0.35
|
|
Concrete
|
2.4-2.5
|
45-50
|
0.3
|
|
GFRP
|
1.4-2.2
|
7-45
|
|
|
Wood, parallel grain
|
0.4-0.8
|
9-16
|
0.2
|
|
Polyimides
|
1.4
|
3-5
|
0.1-0.45
|
|
Nylon
|
1.1 1.2
|
2 4
|
0.25
|
|
PMMA
|
1.2
|
3.4
|
0.35-0.4
|
|
Polycarbonate
|
1.2 1.3
|
2.6
|
0.36
|
|
Natural Rubbers
|
0.83-0.91
|
0.01-0.1
|
0.49
|
|
PVC
|
1.3-1.6
|
0.003-0.01
|
0.41
|
|
7.5
Other Elastic Constants bulk, shear and Lame modulus.
Young’s modulus and Poisson’s ratio are the most common
properties used to characterize elastic solids, but other measures are also
used. For example, we define the shear modulus, bulk
modulus and Lame modulus of an
elastic solid as follows:
A nice table relating
all the possible combinations of moduli to all other possible combinations is
given below. Enjoy!
|
Lame
Modulus
|
Shear
Modulus
|
Young’s
Modulus
|
Poisson’s
Ratio
|
Bulk
Modulus
|
|
|
|
|
|
|
|
|
Irrational
|
|
Irrational
|
Irrational
|
|
|
|
|
|
|
|
|
|
|
|
|
|
|
|
|
|
|
|
|
|
|
|
|
|
|
|
|
|
|
|
|
|
|
|
|
|
|
|
|
|
|
|
|
|
|
|
|
7.6 Physical Interpretation of
elastic constants for isotropic solids
It is important to have a feel for the physical significance
of the two elastic constants E and .
Young’s
modulus E is the slope of the stressstrain curve in
uniaxial tension. It has dimensions of
stress ( ) and is usually large for steel, .
You can think of E as a measure of
the stiffness of the solid. The larger the value of E, the stiffer the solid. For
a stable material, E>0.
Poisson’s ratio
is the ratio of lateral
to longitudinal strain in uniaxial tensile stress. It is dimensionless and
typically ranges from 0.20.49, and is
around 0.3 for most metals. For a stable
material, .
It is a measure of the compressibility of the solid. If ,
the solid is incompressible its volume remains constant, no matter how it
is deformed. If ,
then stretching a specimen causes no lateral contraction. Some bizarre materials have -- if
you stretch a round bar of such a material, the bar increases in diameter!!
Thermal
expansion coefficient quantifies
the change in volume of a material if it is heated in the absence of
stress. It has dimensions of (degrees
Kelvin)-1 and is usually very small.
For steel,
The bulk
modulus quantifies the resistance of the solid to volume changes. It has a large value (usually bigger than E).
The shear
modulus quantifies its resistance to volume preserving shear
deformations. Its value is usually
somewhat smaller than E.
7.7 Strain Energy Density for Isotropic Solids
Note the following
observations
If you
deform a block of material, you do work on it (or, in some cases, it may do
work on you…)
In an
elastic material, the work done during loading is stored as recoverable strain
energy in the solid. If you unload the
material, the specimen does work on you, and when it reaches its initial
configuration you come out even.
The work
done to deform a specimen depends only on the state of strain at the end of the
test. It is independent of the history
of loading.
Based
on these observations, we define the strain
energy density of a solid as the work done per unit volume to deform a
material from a stress free reference state to a loaded state.
To
write down an expression for the strain energy density, it is convenient to
separate the strain into two parts
where, for an isotropic
solid,
represents the strain due
to thermal expansion (known as thermal strain), and
is the strain due to
mechanical loading (known as elastic strain).
Work
is done on the specimen only during mechanical loading. It is straightforward to show that the strain
energy density is
You can also re-write this
as
Observe that