Chapter 13
Plasticity
For
many design calculations, the elastic constitutive equations outlined in
Section 3.1 are sufficient, since large plastic strains are by and large
undesirable and will lead to failure.
There are some applications, however, where it is of interest to predict
the behavior of solids subjected to large loads, sufficient to cause permanent
plastic strains. Examples include:
Modeling metal
forming, machining or other manufacturing processes
Designing crash
resistant vehicles
Plastic design
of structures
Plasticity
theory was developed to predict the behavior of metals under loads exceeding
the plastic range, but the general framework of plasticity theory has since
been adapted to other materials, including polymers and some types of soil
(clay). Some concepts from metal
plasticity are also used in modeling concrete and other brittle materials such
as polycrystalline ceramics.
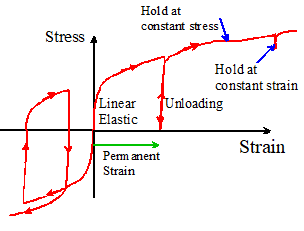
13.1 Features of the inelastic
response of metals.
We
begin by reviewing the results of a typical tension/compression test on an
annealed, ductile, polycrystalline metal specimen (e.g. copper or Al). Assume that the test is conducted at moderate
temperature (less than the melting point of the solid e.g. room temperature) and at modest strains (less
than 10%), at modest strain rates ( ).
The results of such a test
are
For modest
stresses (and strains) the solid responds elastically. This means the stress is proportional to the
strain, and the deformation is reversible.
If the stress
exceeds a critical magnitude, the stressstrain curve
ceases to be linear. It is often
difficult to identify the critical stress accurately, because the stress strain
curve starts to curve rather gradually.
If the critical
stress is exceeded, the specimen is permanently changed in length on unloading.
If the stress
is removed from the specimen during a test, the stressstrain curve
during unloading has a slope equal to that of the elastic part of the stressstrain
curve. If the specimen is re-loaded, it
will initially follow the same curve, until the stress approaches its maximum
value during prior loading. At this
point, the stressstrain curve once
again ceases to be linear, and the specimen is permanently deformed further.
If the test is
interrupted and the specimen is held at constant strain for a period of time,
the stress will relax slowly. If the
straining is resumed, the specimen will behave as though the solid were
unloaded elastically. Similarly, if the
specimen is subjected to a constant stress, it will generally continue to
deform plastically, although the plastic strain increases very slowly. This phenomenon is known as `creep.’
If the specimen
is deformed in compression, the stressstrain curve is a
mirror image of the tensile stressstrain curve (of
course, this is only true for modest strains.
For large strains, geometry changes will cause differences between the
tension and compression tests).
If the specimen
is first deformed in compression, then loaded in tension, it will generally
start to deform plastically at a lower tensile stress than an annealed
specimen. This phenomenon is known as
the `Bauschinger effect.’
Material
response to cyclic loading can be extremely complex. One example is shown in the picture above in this case, the material hardens
cyclically. Other materials may soften.
The detailed
shape of the plastic stressstrain curve
depends on the rate of loading, and also on temperature.
We
also need to characterize the multi-axial response of an inelastic solid. This is a much more difficult experiment to
do. Some of the nicest experiments were
done by G.I. Taylor and collaborators in the early part of the last century. Their approach was to measure the response of
thin-walled tubes under combined torsion, axial loading and hydrostatic
pressure.
The main conclusions of
these tests were
The shape of
the uniaxial stress-strain curve is insensitive to hydrostatic pressure. However, the ductility (strain to failure)
can be increased by adding hydrostatic pressure, particularly under torsional
loading.
Plastic strains
are volume preserving, i.e. the plastic strain rate must satisfy
During plastic
loading, the principal components of the plastic strain rate tensor are
parallel to the components of stress acting on the solid. This sounds obvious until you think about
it… To understand what this means,
imagine that you take a cylindrical shaft and pull it until it starts to deform
plastically. Then, holding the axial
stress fixed, apply a torque to the shaft.
Experiments show that the shaft will initially stretch, rather
than rotate. The plastic strain
increment is proportional to the stress acting on the shaft, not the stress
increment. This is totally unlike
elastic deformation.
Under
multi-axial loading, most annealed polycrystalline solids obey the Levy-Mises
flow rule, which relates the principal components of strain rate during
plastic loading to the principal stresses as follows
In this section, we will outline the simplest
plastic constitutive equations that capture the most important features of
metal plasticity. There are many
different plastic constitutive laws, which are intended to be used in different
applications. There are two broad
classes:
1. Rate independent plasticity which is used to model metals deformed at low
temperatures (less than half the material’s melting point) and modest strain
rates (of order 0.01-10/s). This is the
focus of this section.
2. Rate dependent plasticity, or viscoplasticity used to model high temperature creep (steady
accumulation of plastic strain at contstant stress) and also to model metals
deformed at high strain rates (100/s or greater), where flow strength is
sensitive to deformation rate.
There are also various different models within these
two broad categories. The models
generally differ in two respects (i) the yield criterion; (ii) the strain
hardening law. There is no completely
general model that describes all the features that were just listed, so in any
application, you will need to decide which aspect of material behavior is most
important, and then choose a model that accurately characterizes this behavior.
Key ideas in
modeling metal plasticity
Five
key concepts form the basis of almost all classical theories of
plasticity. They are
1. The decomposition of strain
into elastic and plastic parts;
2. Yield criteria, which
predict whether the solid responds elastically or plastically;
3. Strain hardening rules,
which control the way in which resistance to plastic flow increases with
plastic straining;
4. The plastic flow rule, which
determines the relationship between stress and plastic strain under multi-axial
loading;
5. The elastic unloading
criterion, which models the irreversible behavior of the solid.
These
concepts will be described in more detail in the sections below.
For
simplicity, we will at this stage restrict attention to infinitesimal deformations.
Consequently,
we adopt the infinitesimal strain tensor
as our deformation measure. We have no need to distinguish between the
various stress measures and will use to denote stress.
It is also important to note that the plastic strains in a solid depend on the
load history. This means that
the stress-strain laws are not just simple equations relating stress to
strain. Instead, plastic strain laws
must either relate the strain rate in the solid to the stress and stress rate, or else
specify the relationship between a small increment of plastic strain in terms of strain, stress and stress
increment . In addition, plasticity problems are almost
always solved using the finite element method.
Consequently, numerical methods are used to integrate the plastic
stress-strain equations.
13.2. Decomposition of strain into
elastic and plastic parts
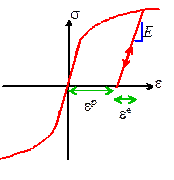
Experiments show that under uniaxial loading, the
strain at a given stress has two parts: a small recoverable elastic strain, and
a large, irreversible plastic strain, as shown in the picture. In uniaxial tension, we would write
Experiments suggest that the reversible part is
related to the stress through the usual linear elastic equations. Plasticity theory is concerned with
characterizing the irreversible part.
For multiaxial loading, we generalize this by
decomposing a general strain increment into elastic and plastic parts (as well as an
optional thermal expansion), as
The
elastic part of the strain is related to stress using the linear elastic
equations
The thermal
strain is
13.3
Yield Criteria
The
yield criterion is used to determine the critical stress required to cause
permanent deformation in a material. There
are many different yield criteria here we will just list the simplest ones. Let be the stress acting on a solid, and let denote the principal values of stress. In addition, let denote the yield stress of the material in
uniaxial tension. Then, define
VonMises yield
criterion
Tresca yield criterion
In
both cases, the criteria are defined so that the material deforms elastically
for ,
and plastically for . The yield stress may increase during plastic straining, so we
have shown that Y is a function of a
measure of total plastic strain ,
to be defined in below.
An alternative form of VonMises criterion.
For a general stress state, it is a nuisance having to compute the principal
stresses in order to apply von Mises yield criterion. Fortunately, the criterion can be expressed
directly in terms of the stress tensor
where
are the components of the
`von Mises effective stress’ and
`deviatoric stress tensor’ respectively.
These yield criteria are
based largely on the following experimental observations:
(1) A
hydrostatic stress (all principal stresses equal) will never cause yield, no
matter how large the stress;
(2) Most polycrystalline metals are isotropic. Since the yield criterion depends only on the
magnitudes of the principal stresses, and not their directions, the yield
criteria predict isotropic behavior.
Tests
suggest that von Mises yield criterion provides a slightly better fit to
experiment than Tresca, but the difference between them is very small. Sometimes it simplifies calculations to use
Tresca’s criterion instead of von Mises.
13.4 Graphical representation of the
yield surface.
Any arbitrary stress state can be plotted in `principal stress space,’ with the three
principal stresses as axes.
The
VonMises yield
criterion is plotted in this way in the picture to the right. The yield criterion is a cylinder, radius ,
with its axis parallel to the line
If
the state of stress falls within the cylinder, the material is below yield and
responds elastically. If the state of
stress lies on the surface of the cylinder, the material yields and deforms
plastically. If the plastic deformation
causes the material to strain harden, the radius of the cylinder
increases. The stress state cannot lie
outside the cylinder this would lead to an infinite plastic strain.
Because
the yield criterion defines a surface in stress space, it is often
referred to as a yield surface. The
yield surface is often drawn as it would appear when viewed down the axis of
the cylinder, as shown below. The Tresca yield criterion can also be plotted in
this way. It looks like a cylinder with
a hexagonal cross section, as shown.
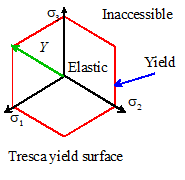
13.5. Strain hardening laws
Experiments show that if you plastically deform a
solid, then unload it, and then try to re-load it so as to induce further
plastic flow, its resistance to plastic flow will have increased. This is known as strain hardening.
Obviously, we can model strain hardening by relating
the size and shape of the yield surface to plastic strain in some appropriate
way. There are many ways to do
this. Here we describe the two simplest
approaches.
Isotropic
hardening
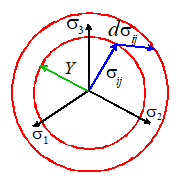
Rather obviously, the easiest way to model strain
hardening is to make the yield surface increase in size, but remain the same
shape, as a result of plastic straining.
This means we must devise some appropriate
relationship between Y and the plastic strain. To get a suitable scalar measure of plastic
strain we define the accumulated plastic strain magnitude
(the factor of 2/3 is introduced so that in a uniaxial tensile test in which the
specimen is stretched parallel to the direction.
To see this, note that plastic strains do not change volume, so that and substitute into the formula.)
Then we make Y
a function of . People often use power laws or piecewise
linear approximations in practice. A few of the more common forms of hardening
functions are
Perfectly plastic
solid:
Linear strain hardening
solid:
Powerlaw hardening
material:
In
these formulas,
, h and m are material properties. These functions are illustrated in the
figures below
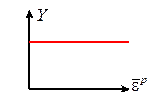
|
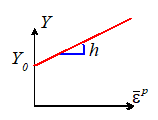
|
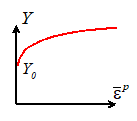
|
Perfectly plastic solid
|
Linear strain hardening solid
|
Power-law hardening solid
|
Kinematic
hardening
An isotropic hardening law is generally not useful
in situations where components are subjected to cyclic loading. It does not account for the Bauschinger
effect, and so predicts that after a few cycles the solid will just harden
until it responds elastically.
To fix this, an alternative hardening law allows the
yield surface to translate, without changing its shape. The idea is illustrated graphically in the
picture. As you deform the material in
tension, you drag the yield surface in the direction of increasing stress, thus
modeling strain hardening. This softens
the material in compression, however.
So, this constitutive law can model cyclic plastic deformation. The stress-strain curves for isotropic and
kinematic hardening materials are contrasted in the figure on the right.
To account for the fact that
the center of the yield locus is at a position in stress space, the Von-Mises yield criterion
needs to be modified as follows
Here, Y is
now a constant, and hardening is modeled by the motion of the yield surface. To
do so, we need to relate to the plastic strain history somehow. There are many ways to do this, which can
model subtle features of the plastic response of solids under cyclic and
nonproportional loading. The simplest approach is to set
.
This
hardening law predicts that the stress-plastic strain curve is a straight line
with slope c. This is known as linear
kinematic hardening.
A
more sophisticated approach is to set
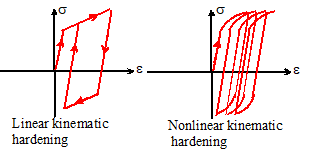
where c and are material constants. It’s not so easy to visualize what this does it turns out that that this relation can model
cyclic creep the tendency of a material to accumulate
strain in the direction of mean stress under cyclic loading, as illustrated in
the figure on the right. It is known as
the Armstrong-Frederick hardening law.
There are many other kinematic type hardening laws. New ones are still being developed.
13.6
The plastic flow law
To complete the plastic stress-strain relations, we
need a way to predict the plastic strains induced by stressing the material
beyond the yield point. Specifically,
given
1. The current stress applied to the material
2. The current yield stress
(characterized by for isotropic hardening, or for kinematic hardening)
3. A small increase in stress applied to the solid
we wish to determine the small change in plastic strain
.
The formulas are given below, for isotropic and
kinematic hardening. These are just fits
to experiment (specifically, to the Levy-Mises flow rule). The physical significance and reason for the
structure of the equations will be discussed later.
The plastic strains are usually derived from the
yield criterion f defined in 3.6.3,
and so are slightly different for isotropic and kinematic hardening. A material that has its plastic flow law
derived from f is said to have an
`associated’ flow law i.e.the flow law is associated with f.
Isotropic Hardening (Von-Mises yield
criterion)
where
denotes the Von-Mises yield criterion, and is determined from the condition that the
yield criterion must be satisfied at all times during plastic straining. This shows that
Here, is
the slope of the plastic stress-strain curve.
The algebra involved in differentiating f with respect to stress is outlined below.
Linear Kinematic Hardening (Von-Mises
yield criterion)
where
the yield criterion is now
and as before is determined from the condition that the
yield criterion must be satisfied at all times during plastic straining. This shows that
Recall
that for linear kinematic hardening the hardening law is
Substituting
into the Taylor
expansion of the yield criterion and simplifying shows that
Comparison
of flow law formulas with the Levy-Mises flow rule
The
Levy-Mises flow law (based on experimental observations) states that principal
values of the plastic strain increment induced by a stress increment are related to
the principal stresses by
It
is straightforward to show that this observation is consistent with the
predictions of the flow law formulas given in this section. To see this,
suppose that the principal axes of stress are parallel to the directions.
In this case the only nonzero components of deviatoric stress are
The flow law
gives
Thus,
we see that
with
similar expressions for other components.
Some trivial algebra then yields the Levy-Mises flow law.
Differentiating
the yield criterion
Differentiating
the yield criterion requires some sneaky index notation manipulations. Note
that
Now, recall that
and further that
Hence
and
However, observe that
so that
and finally
13.7 The
Elastic unloading condition
There is one final issue to
consider. Experiments show that plastic
flow is irreversible, and always dissipates energy. If the increment in stress is tangent to the yield surface, or brings the
stress below yield, as shown in the picture then there is no plastic strain.
For an
isotropically hardening solid, this unloading condition may be expressed as
For
kinematic hardening,
In
both cases, the solid deforms elastically (no plastic strain) if the condition
is satisfied.
13.8
Complete incremental stress-strain relations for a rate independent
elastic-plastic solid
We
conclude by summarizing the complete elastic-plastic stress strain relations
for an isotropic solid with Von-Mises
yield surface.
Isotropically
hardening elastic-plastic solid
The solid is characterized by its elastic constants and by the yield stress as a function of accumulated plastic strain and its slope
In
this case we have that
with
where
These
may be combined to
It
is sometimes necessary to invert these expressions. A straightforward but tedious series of index
notation manipulations shows that
This constitutive law is
the most commonly used model of inelastic deformation. It has the following properties:
It will
correctly predict the conditions necessary to initiate yield under multiaxial
loading
It will
correctly predict the plastic strain rate under an arbitrary multiaxial stress
state
It can model
accurately any uniaxial stressstrain curve
It has the following
limitations:
It is valid
only for modest plastic strains (<10%)
It will not
predict creep behavior or strain rate sensitivity
It does not
predict behavior under cyclic loading correctly
It will not
predict plastic strains accurately if the principal axes of stress rotate
significantly (more than about 30 degrees) during inelastic deformation
Linear
Kinematically hardening solid
The solid is characterized by its elastic constants and by the initial yield stress and the strain hardening rate c. Then,
with
where
Finally, the evolution equation for is
This
constitutive equation is used primarily to model cyclic plastic deformation, or
plastic flow under nonproportional loading (where principal axes of stress
rotate significantly during plastic flow). It has the following limitations:
It is valid only for modest plastic strains
(<10%)
It will not predict creep behavior or strain
rate sensitivity
It does not predict the shape of the
stress-strain curve accurately
13.9 Typical values for yield stress of
polycrystalline metals
Unlike
elastic constants, the plastic properties of metals are highly variable, and
are also very sensitive to alloying composition and microstructure (which can
be influenced by heat treatment and mechanical working). Consequently, it is impossible to give
accurate values for yield stresses or hardening rates for materials. The table below (again, taken from
`Engineering Materials,’ by M.F. Ashby and D.R.H. Jones, Pergamon Press) lists
rough values for yield stresses of common materials these may provide a useful guide in
preliminary calculations. If you need
accurate data you will have to measure the properties of the materials you plan
to use yourself.
Material
|
Yield
Stress
|
Material
|
Yield
Stress
|
Tungsten Carbide
|
6000
|
Mild steel
|
220
|
Silicon Carbide
|
10
000
|
Copper
|
60
|
Tungsten
|
2000
|
Titanium
|
180
- 1320
|
Alumina
|
5000
|
Silica glass
|
7200
|
Titanium Carbide
|
4000
|
Aluminum & alloys
|
40-200
|
Silicon Nitride
|
8000
|
Polyimides
|
52
- 90
|
Nickel
|
70
|
Nylon
|
49
- 87
|
Iron
|
50
|
PMMA
|
60
- 110
|
Low alloy steels
|
500-1980
|
Polycarbonate
|
55
|
Stainless steel
|
286-500
|
PVC
|
45-48
|
13.10 Thin walled tube under combined
tension and torsion
It is
usually difficult to solve boundary value problems for plastically deforming
solids, because the stress-strain law is nonlinear, and history dependent. Finite element calculations can handle both
without difficulty. But it is helpful
to solve a few example problems for solids with simple geometries and loading
to illustrate how the stress-strain laws work.
The figure
shows a thin walled tube with cross-sectional area . It
is made from an elastic-plastic solid with elastic constants , yield stress Y and hardening slope . It
is loaded by axial force P and torque
Q.
Calculate the plastic strain rate in the tube.
1. The stress in the tube is ; all other components zero.
2. The hydrostatic stress is
3. The deviatoric stresses follow as
4. The Von-Mises effective stress is
therefore
5. We can use the sress-strain rate
formulas to calculate the strain rate
The quantity
There are
some surprising features of these results.
For example, notice that if the tube is first deformed by a force P, and is then twisted (so that ) the tube will experience an axial plastic
stretch before it starts to twist. This
is because the direction of the plastic strain rate is parallel to the
deviatoric stress, not the stress rate.
13.11 Elastic-perfectly plastic hollow
sphere subjected to monotonically increasing internal pressure
Assume
that
The sphere is stress free before it is loaded
No body forces act on the sphere
The sphere has uniform temperature
The inner surface r=a is subjected to (monotonically increasing) pressure
The outer surface r=b is traction free
Strains are infinitesimal
Solution:
(i) Preliminaries:
The sphere first reaches yield (at r=a) at an internal pressure
For pressures in the range the region between and deforms plastically; while the region between remains elastic, where c satisfies the equation
At a pressure the entire cylinder is plastic. At this point the sphere collapses the displacements become infinitely large.
(ii) Solution in the plastic region
(iii) Solution in the elastic region
These results
are plotted in the figures below.
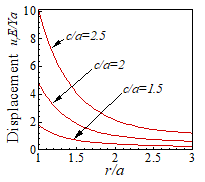
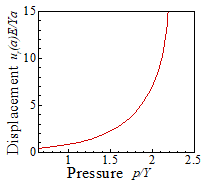
(a)
(b)
(c)
(a) Stress and (b) displacement
distributions for a pressurized elastic-perfectly plastic spherical shell; and
(c) Displacement at r=a as a function
of pressure. Displacements are shown for
Derivation: By substituting the stresses for the
elastic solution given in 4.1.4 into the Von-Mises yield criterion, we see that
a pressurized elastic sphere first reaches yield at r=a. If the pressure is increased beyond yield we anticipate that a
region will deform plastically, while a region remains elastic. We must find separate solutions
in the plastic and elastic regimes.
In the plastic regime
(i) We anticipate that .
The yield criterion then gives .
(ii) Substituting this result into the equilibrium equation
given in Sect 4.2.2 shows that
(iii) Integrating, and using the boundary condition together with the yield condition (i) gives
(iv) Since the pressure is monotonically increasing, the
incremental stress-strain relations for the elastic-plastic region given in
4.2.2 can be integrated. The elastic strains follow as
(v) The plastic strains satisfy . Consequently, using the strain partition
formula, the results of (iv), and the strain-displacement relation shows that
(vi) Integrating gives
where C is a
constant of integration
(vii) The constant of integration can
be found by noting that the radial displacements in the elastic and plastic
regimes must be equal at r=c. Using the expression for the elastic
displacement field below and solving for C gives
This result can be simplified by noting
that from the expression for the location of the
elastic-plastic boundary given below.
In the elastic regime
The solution can be found directly
from the solution to the internally pressurized elastic sphere given in Sect
4.1.4. From step (iii) in the solution
for the plastic regime we see that the radial pressure at r=c is .
We can simplify the solution by noting from the expression for the location of the
elastic-plastic boundary. Substituting
into the expressions for stress and displacement shows that
Location of the elastic-plastic boundary
Finally, the elastic-platsic boundary
is located by the condition that the stress in the elastic region must just
reach yield at r=c (so there is a
smooth transition into the plastic region).
The yield condition is ,
so substituting the expressions for stress in the elastic region and
simplifying yields
If ,
Y, a and b are specified this equation can be solved (numerically) for c.
For graphing purposes it is preferable to choose c and then calculate the corresponding value of