Brown Shock Tube

The Brown Shock Tube is a multi-purpose instrument for high-temperature, high-pressure gas-phase measurements. The entire shock tube was first designed in SolidWorks with guidance from ASME Boiler and Pressure Vessel Code.

Driven Section The driven section has an internal diameter of 4 inches (10 cm) and an adjustable length, currently 24 feet (7.3 m) and can withstand static pressures in excess of 100 bar. The flanges that connect the driven sections were custom designed to operate over pressures ranging from high vacuum to 100 bar. The entire driven section and gas manifold assembly have been chemically passivated SilcoNert 2000. The inlet gas port is based on a design from Eric Petersen of Texas AM.
Driver Section Unlike most shock tubes, the Brown Shock Tube operates without a diaphram. It uses a fast-acting value, based upon a design of Robert Tranter at ANL. The inner diameter of the driver section is 15.5 inches (39 cm) and can withstand pressures up to 18 atm. The advantage of the diagphragmless system is fast operation (one shock every 2 minutes) and high reproducibility. The disadvantage is weaker shocks. For high-strength shocks, we use a double-diaphragm system, based upon a design of Nabiha Chaumeix (CNRS-Orleans). The diaphragm system will use driver components with identical specifications to the driven system in terms of diameter and strength.
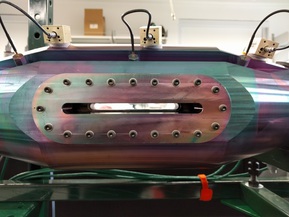
Diagnostics The shock tube has been designed with multiple diagnostics. Currently we use laser-schlieren densitometry in the incident shock to measure the rate of decomposition in the first ~10 microseconds after the passage of the shock. The shock tube is also equiped for more conventional diagnostics in the reflected shock, including laser-absorption spectroscopy for species quantification and pressure trace measurement for ignition delays. We're in the process of designing a fast-acting sampling value for single-pulse studies.