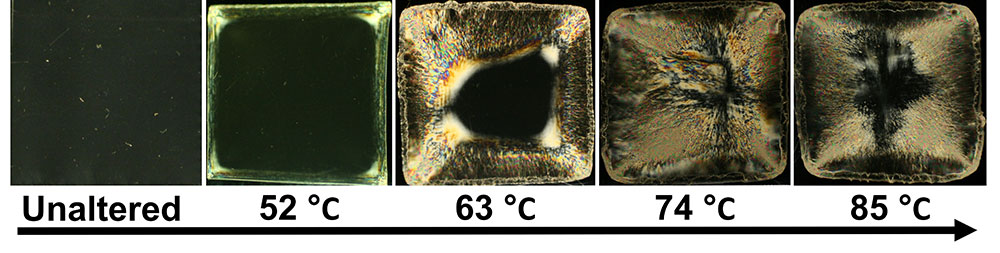
Treating polylactic acid, a commonly used polymer material, with heat and pressure creates crystals and causes polymer strands to become more organized. Those changes could make the material more useful in medical applications. Mathiowitz lab / Brown University
PROVIDENCE, R.I. [Brown University] — Polylactic acid, or PLA, is a biodegradable polymer commonly used to make a variety of products from disposable cups to medical implants to drug delivery systems. A team of Brown University researchers has shown that by treating PLA at various temperatures and pressures, they can induce a new polymer phase in the material — one that could possibly decrease the rate at which it degrades.
“It’s an exciting finding from the standpoint of basic science, in that we’ve found a new polymer phase and have identified a method for inducing it,” said Edith Mathiowitz, a professor of medical science and engineering at Brown. “In terms of applications, the polymer we worked with in this study has many uses, and we believe the properties we have discovered now will allow us to make it better.”
The findings are published in the journal Polymer.
PLA is a semi-crystalline material, meaning parts of the material’s molecular structure are ordered into crystals while the rest is disordered, or amorphous, like glass. Work by previous researchers had shown that treating PLA with heat could increase the material’s crystalline makeup, which could help to increase its strength. Researchers in Mathiowitz’s lab, led by doctoral candidate and U.S. Navy veteran Christopher Baker, wanted to see if adding pressure to the treatment process would further influence the material’s structure.
Baker treated PLA samples under a variety of different temperature and pressure conditions for varying amounts of time. Pressures ranged from 2,000 to 20,000 pounds per square inch. Temperatures used for treatments were above, below and nearly equal to the glass transition temperature for PLA — the temperature at which the amorphous parts of the material transition from solid to rubbery.
Baker showed that the treatments increased the amount of crystalline area in the material, but there was another more surprising finding. At higher temperatures and pressures, the amorphous parts of the material became birefringent, meaning that they bend light differently depending upon how the light is polarized. That is an indicator of a substantial structural change in the amorphous portions of the material.
Generally speaking, birefringence is a property found in crystalline materials, so seeing it in the amorphous regions of PLA was a surprise. “We didn’t expect it to have such properties,” Mathiowitz said. “So to see it in the amorphous phase was really amazing.”
Baker then used several methods to further characterize how the amorphous regions had changed. Using a technique called X-ray diffraction, he showed that polymer strands in some of the amorphous sections had become dramatically more ordered.
“The polymer strands are normally a tangled mess,” Baker said. “But we found when we processed the material that the amorphous region became less entangled and much more oriented in a particular direction.”
Further thermal analysis showed that the more ordered sections had a higher glass transition temperature. In general, amorphous materials with higher glass transition temperatures degrade at significantly slower rates.
The new amorphous phase combined with the overall increase in crystallinity in the treated samples could have significant implications for the material’s mechanical properties, the researchers said. The higher crystallinity could make it stronger, while the more ordered amorphous sections could make it last longer. That slower rate of degradation could be particularly useful in medical applications, an area in which Mathiowitz’s lab specializes.
For example, PLA is used as a coating for time-release pills and implantable drug delivery systems. If the rate at which PLA degrades can be controlled, the rate at which it delivers a drug can be altered. There is also interest in using PLA for plates and screws used to stabilize broken bones. The advantage to PLA implants is that they degrade over time, so a patient would not need a second surgery to remove them. PLA may degrade too quickly for some of these applications, but if this new polymer phase slows degradation, it may become a better option.
“Now that we’ve shown that we can intentionally induce this phase, we think it could be very useful in many different ways,” Mathiowitz said.
The researchers plan more research aimed at quantifying changes in material properties as well as investigating whether this phase can be induced in other semi-crystalline materials.